As the pace of change in industrial environments accelerates, we find ourselves at a crossroads, as physical AI steps in.
Warehouses and factories – once defined by static layouts and reactive systems – are beginning to reveal new layers of intelligence, thanks to the convergence of artificial intelligence and digital twin technologies. But this isn’t just about efficiency gains or incremental upgrades. It’s about reimagining how we perceive space, flow, and decision-making in the environments that underpin our physical economy.
This is the case with Physical AI. It refers to artificial intelligence systems designed to perceive, understand, and act within the real world. Unlike traditional AI, which often works behind the scenes analyzing data, Physical AI is deployed in physical environments. factories, warehouses, streets, and even remote terrain.
At Younite, we see AI not as a tool to automate yesterday’s tasks, but as a living collaborator—one that learns, adapts, and evolves alongside human ingenuity. When combined with digital twins—high-fidelity, real-time virtual counterparts of physical environments—we begin to craft a methodology that allows these complex systems to speak back to us, offering insight, foresight, and new forms of interaction.
This means AI isn’t just making decisions on a server. It’s guiding robots, drones, autonomous vehicles, and intelligent cameras to navigate complex spaces, respond to anomalies, and collaborate with humans in real time.
Simulation as a Design Material
Our approach begins with simulation. Through digital replicas of real-world environments, we can stage thousands of what-if scenarios: how materials move, where bottlenecks form, what patterns emerge under different conditions. This process reveals not just the current state of operations, but the potential paths they might take. The AI models trained within these digital twins begin to form a deeper understanding of context: learning from the simulated before acting in the real.
From Fixed Processes to Adaptive Systems
In place of rigid workflows, we advocate for adaptive systems that grow more intelligent over time. By using AI to continuously observe and interpret factory or warehouse behavior, we can begin to uncover signals that were previously invisible. This creates a dynamic loop: data feeds simulation, simulation refines behavior, and behavior generates new data. The factory floor becomes an organism – living, learning, and increasingly self-aware.
A Foundation for Broader Transformation
This isn’t about warehouse logistics alone. The philosophical underpinnings of this methodology can ripple outward to touch nearly every corner of industrial life:
- Production lines become places of exploration, where layout and timing can be fluid, shaped by real-time insight rather than fixed assumptions.
- Maintenance evolves into a more symbiotic relationship with machines—where downtime is predicted rather than endured.
- Training becomes immersive and consequence-free, allowing workers to explore, fail, and grow within virtual environments that mirror the real.
- Planning becomes a matter of creative iteration—where digital twins allow for spatial storytelling and experimentation long before a single machine is moved.
Toward a More Harmonious Industrial Intelligence
There is, of course, a pragmatic business case here: reduced costs, better decisions, sustainability gains. But perhaps more importantly, this methodology reflects a shift in mindset: from control to collaboration, from efficiency to empathy with systems, from design for industry to design with it.
At Younite, we don’t see AI as the end of human-driven processes. We see it as the beginning of a new dialogue between people, machines, and the environments we shape together.
You may also like...
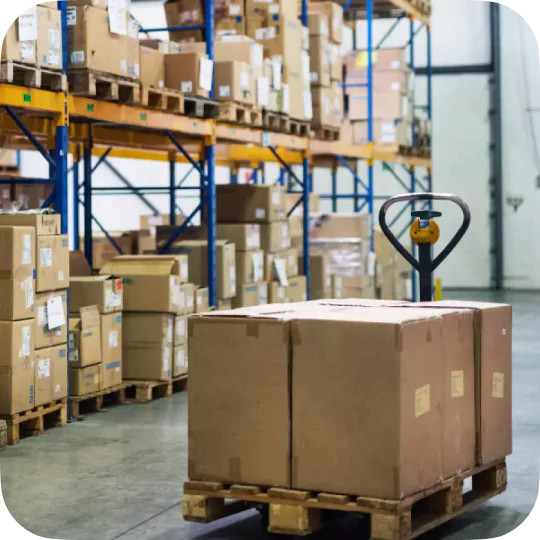
DIGITAL TWIN • INDUSTRIAL AI • INSIGHTS