There’s something wonderfully deceptive about the idea of a digital twin.
On the surface, it sounds so straightforward. Take something from the real world, an object, a place, even a process, and recreate it digitally so you can interact with it, simulate it, study it, or share it.
In reality? It’s anything but simple.
Behind every polished 3D model you see spinning in a browser or powering a slick AR experience is a messy, multi-step process that blends precision, creative problem-solving, and a surprising amount of trial and error. Whether it’s a rare industrial machine, a product prototype, or even a piece of architecture, turning a real-world object into a responsive, optimized digital version is a challenge that’s part science, part craft.
Let’s pull the curtain back on how it really comes together.
Capture: More Than Just a Scan
Everything starts with capturing the object. Depending on the scale and complexity, this could involve photogrammetry (lots of overlapping photos), laser scanning, LiDAR, structured light scanning, or even a combination.
The goal is simple in theory. Just document every angle and surface detail with enough accuracy that a computer can reconstruct it in 3D. But in practice, this part is full of surprises. You’re constantly dealing with reflective surfaces, awkward lighting, hidden crevices, and the simple challenge of physically accessing all sides of an object that maybe wasn’t designed to be moved, or even touched.
You learn quickly that capturing reality isn’t just about the gear. It’s about knowing how to see. How to understand how light, texture, and shape interact, and how they’ll behave once they leave the physical world.
Reconstruction: When Reality Hits the Render Engine
Once you’ve captured your data, you feed it into software that tries to make sense of it all. This is where your raw inputs in the form of photos, point clouds, and depth data get translated into something 3D.
The first outputs are usually rough. Shapes might be warped, edges can be messy, textures might look muddy. But hidden in there is the beginning of a faithful digital version of the object.
This is the phase where you go from “I think we got it” to “Okay, now we make it usable.”
Cleanup and Refinement: The Craft Kicks In
Now the real hands-on work begins. The raw 3D model gets passed to a digital artist or technical designer who begins the painstaking process of cleaning it up.
This could mean fixing mesh errors, re-topologizing surfaces, rebuilding missing sections, and correcting any anomalies caused by lighting, shadows, or environmental interference during the capture phase. It’s a balancing act between staying true to the original and making something that’s clean and consistent enough to actually use.
And then there’s the textures. This may involve repainting or refining surface detail so the digital version doesn’t just look accurate, but feels believable when viewed up close or under dynamic lighting.
It’s not glamorous work, but it’s where the magic really happens.
Optimization: Making It Perform, Not Just Look Good
Even the most detailed digital twin is useless if it grinds to a halt the moment it loads.
That’s why optimization is such a crucial step. You simplify geometry, compress assets, streamline materials, and make the model efficient enough to run in real time whether its being delivered in a game engine, AR app, or simulation platform.
This is also when you start thinking about how and where this twin will be used. Is it going into a mobile app? Will it live in VR? Will it be used for training simulations, or integrated into an interactive exhibit? Each destination has different constraints and opportunities, so optimization isn’t just technical—it’s strategic.
Activation: Turning the Model Into a Living Experience
With the model prepped and optimized, it’s ready to be dropped into a real-time environment. And this is where it transforms from a digital sculpture into something alive.
Now you can layer on interactions—things like clickable hotspots, simulations, animations, or spatial audio. You add logic, lighting, context. Maybe you build a guided walkthrough, or maybe it becomes something people explore freely, on their terms.
This is where the digital twin starts to fulfill its real purpose. It’s not just a copy of a thing anymore. It’s now a tool for understanding, engaging, learning, or even entertaining.
What You End Up With Is So Much More Than a Replica
The final result is often used in ways the original physical object never could be.
It can be shared instantly with people on the other side of the world. It can be placed into training environments, shown off in product demos, analyzed in simulations, or even modified in ways that let teams explore future possibilities. It becomes a platform—not just a representation.
It's worth reminding ourselves that no two digital twins are ever the same, because no two reasons for making them are ever quite the same.
Each one starts with a real-world object, but ends with a purpose all its own.
Let's Younite
Connect with us and discover how Younite can help your organization turn your physical assets into ever-lasting flexible digital twins? Get in touch!
Contributors
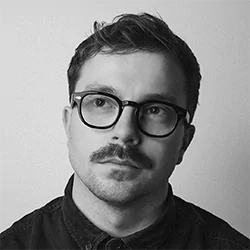
Miika Niemelä
Senior Project Manager
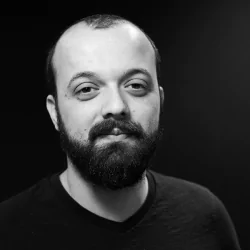
Emerson Rosa
Technical 3D Artist
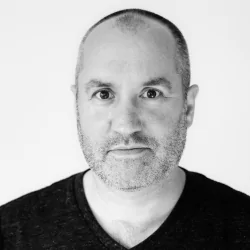
Dave Papworth
CCO
You may also like...
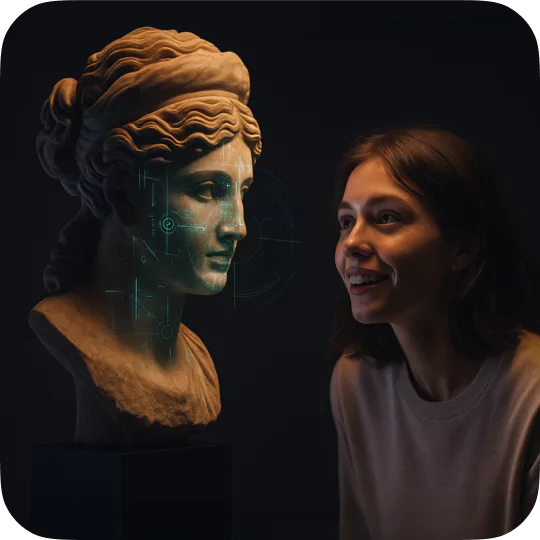
CREATIVE AI • DIGITAL TWIN • UX